LOCAL BUSINESS
Method Mfg receives Innovation Award for aerospace manufacturing
Custom machine parts are in high demand, and in response to that need, Rhys Andersen created Method Mfg, a cutting-edge precision manufacturing company in Buda, from the ground up. The shop started with a broken machine, which Andersen had to rebuild himself, and has evolved into a high-demand company that makes custom machined parts for the aerospace industry.
“What we started with was actually producing large parts that nobody in the Austin area was making at the time because one of our customers was saying that they couldn't find anybody outside of California that could do that type of part for them,” Andersen said. “From there, we did the same thing over and over again — communicating with our customers, finding out where their painpoints were and building a process around the kind of stuff that they needed and that they struggled to source locally.”
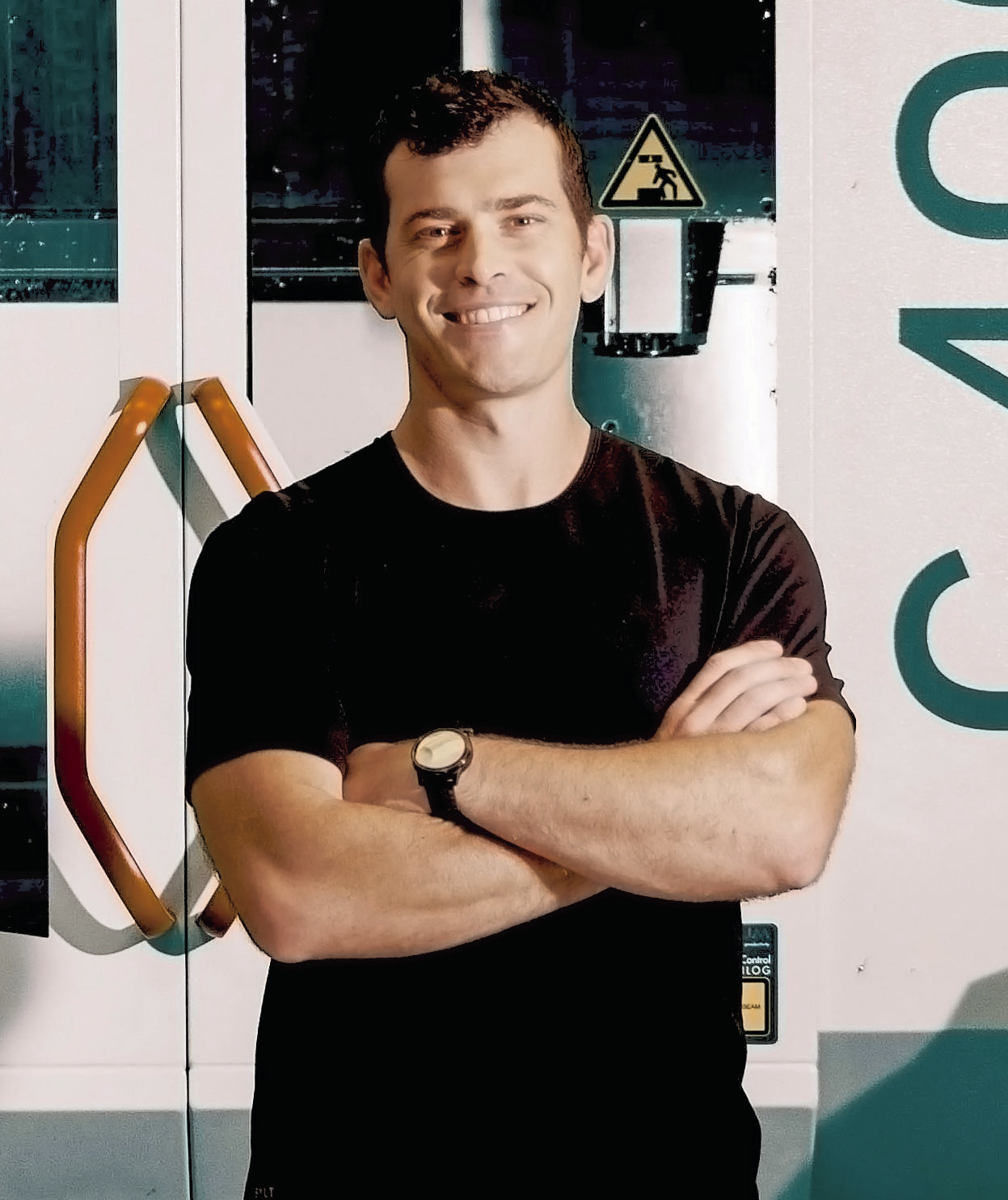
The parts Custom Mfg makes have evolved over time.
“Now, we're one of the prime suppliers making machine components for the next generation space suits that are going to go to the moon,” Andersen said. “We're machining a lot of really complicated components that a lot of other shops just don't have the capability to handle.”
Custom Mfg is not your typical dirty production warehouse, and there is a focus on employee satisfaction that enables them to recruit the type of employees that they’re looking for.
“My team is working with the latest software like AI tools, and the latest five axis machines. Then they're also working in an environment that's very clean,” Andersen said. “We also give our employees a huge amount of autonomy, so I don't have set hours and shifts that people show up to. It's really about the team communicating what needs to get done and when, and we just get it done. What we're trying to do here is create an environment that draws people into it, and attracts the kind of person that's excited about the level of work that we're doing.”
Andersen this approach has led to a team filled with dedicated and driven employees.
“They're not only just machining parts, but they're working with our clients to provide manufacturability feedback on the components,” Andersen said. “That's really critical to the life cycle of a lot of these projects we're working on, not only from the standpoint of just delivering a better product but also allowing those companies to continue to innovate.”
Andersen said the process of machining custom parts starts with computer design but other factors need to be considered to ensure a lasting product.
“They're solving a puzzle. So for the end result, they want it to look like what's on the screen, but they have to balance out everything from tool life to material removal... so that when that part is in its final form, it's within the tolerances. My guys have come up with really creative solutions for some pretty challenging parts that have to be stress relieved in a certain way so that the part doesn't deform. And that's really where the challenge of machining is,” Andersen said. “They think you kind of just hit a button, and it appears. There's a lot of thought that goes into the fixturing, the material removal and all that stuff. And that's kind of the secret sauce of where having really skilled and creative guys comes into play.”
Andersen has been building equipment since he was young when he would contribute to his family’s sewer business in Montana.
“We built equipment for that business that kind of evolved into building equipment for the Forest Service, and I grew up making stuff,” Andersen said, adding that when he moved to Texas he saw an opportunity for machining parts for the semiconductor industry. “We bought a machine out of the oil field to make these large parts, and it ended up being a lot more challenging than we thought. The machine didn't actually work when we got it, so I had to rebuild the machine myself. Then we gradually built that confidence with our customers… Because we were working in a very technical area, it just made jumping into aerospace and these other sectors very easy for us. Our first client we started out with that really brought us into the industry had really high expectations, and that just made us a better machine shop.”
Initially, the company was something completely different but evolved into what it is today.
“We originally existed in 2014 as an architectural fabrication company, and then in 2018 is when we bought our first machine and started making that shift,” Andersen said. “Now we don't do any welding or any fabrication; it's all machined parts.”
Method Mfg won the Innovation Award at the recent Innovation Summit held by the Greater San Marcos Partnership, and Andersen was surprised but felt it validated their hard work.
“We worked really hard, and for somebody to notice it — that's amazing. It tells us we're on the right path,” Andersen said. “It’s not always easy doing it your own way or trying to improve on something. It's just meant a lot to have somebody recognize that we're over here working really hard and that, for the [relatively small] size of the company, we're taking on extremely challenging projects.”
Learn more about the company at methodmfg. com.